Background:
Working in support of a large U.S. steel manufacturer, a manufacturer of custom, heavy-duty industrial machinery for use in metals and manufacturing industries needed a reliable method of holding a 70-ton rail-mounted ladle preheater stationary. To achieve this goal, the project required an industrial disc brake capable of resisting the full output torque of two gearmotors to be mounted directly to the ladle car idler shaft.
Given Hindon’s experience providing application-specific engineered industrial braking solutions across industries, including in the steel mill industry, Hindon was a natural fit to support the customer with the braking aspect of their project.
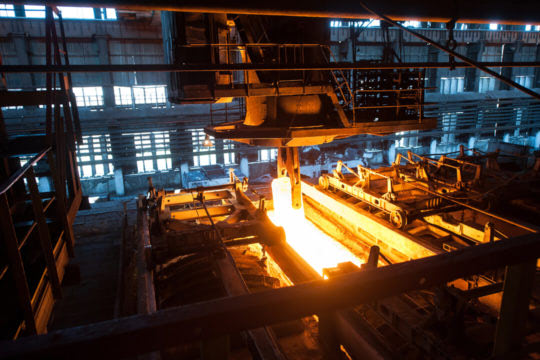
A steel mill environment typically has a dusty, abrasive atmosphere with ambient temperatures reaching over 140°F.
Application Challenges:
- High torque requirement in space constrained envelope
- Changing steel mill environment – high ambient temperature, dusty abrasive atmosphere
- High duty cycle requirement
Solution:
After understanding the customer’s project goals, constraints, and technical requirements, Hindon explored a range of potential braking solutions with the customer including a pneumatically released brake and several different electrically released brake designs ranging from single caliper to multiple caliper arrangements.
After collaborating with the customer on several system design iterations, Hindon ultimately designed and supplied brake system involving two spring-applied electromagnetically released disc brakes. The electromagnetic fail-safe brakes came equipped with a rectifier for control of the brakes. This solution was designed to meet/exceed the duty cycle requirement for the application, the high ambient temperature requirement (up to 140 °F), and the torque requirement (~6,000 Nm), all while fitting within the space available in this retrofit application.
Hindon delivered the industrial braking system within the project schedule, avoiding any delays to the end user’s project completion timeline. Furthermore, Hindon’s braking system worked exactly as intended within the context of the customer’s overall solution, providing a robust, reliable, and cost-effective solution that increased both safety and productivity at this large U.S. steel producer’s operation.