Bearings are the lifeblood of an industrial vibrator. Assuming a vibrator has been properly sized for an application and mounted correctly, bearing maintenance will likely determine the life you get out of the vibrator.
In this blog, we’ll share our thoughts on what’s important when it comes to bearings for rotary electric industrial vibrators.
Industrial Vibrator Bearing Overview
Cylindrical Roller Bearings
While not all industrial vibrators use cylindrical roller bearings, most heavy-duty rotary electric vibrators incorporate this type of bearing. Sealed ball bearings are generally appropriate for smaller vibrator motors and require virtually no maintenance. For the purposes of this blog topic, we’ll be talking about NJ 2306 cylindrical roller bearing sizes and larger (up to NJ 2326).
Factory-Specified Bearings
While industrial vibrators are often associated with static electrical motors, they are actually very unique pieces of equipment. One obvious, but important, difference is that industrial vibrators are designed to shake violently, making them much less forgiving than other types of electrical motors when it comes to maintenance and repair. What does this mean when it comes to bearings? Use the factory specified bearing.
We often see people who are familiar with industrial motors, like electric motor repair shops, get this wrong. It’s easy to think that the bearing you used in vibrator manufacturer A’s repair will work when repairing vibrator manufacturer B’s motor, but there are subtle differences that absolutely make a difference with industrial vibrators.
One such detail that is often overlooked is whether a vibrator requires a bearing with a C3 or C4 fit. The fit refers to internal radial clearance between the rollers and inner ring of the outer race. This is critical for vibrator motors because they are required to operate at higher temperatures than standard electric motors.
Another detail that’s easy to overlook is whether you should use brass or polyamide (phenolic resin) caged bearings. In many cases, polyamide caged bearings are fine, but brass caged bearings are better suited for some more arduous applications.
Hindon/Invicta Standard Bearings
Hindon/Invicta Vibrators use SKF and FAG brand bearings, as they are the worldwide standard for cylindrical roller bearings. One advantage of these high-quality brands is that their roller bearings contain specific logarithmic profiled tapered rollers that allow for inherent shaft deflection when the vibrator is in operation. Many other bearings do not contain these slightly tapered rollers which can cause edge stressing and prematurely fail the bearings.
We specify an “NJ” type, which has a shouldered inner race, along with the “E” and “XL” designations, which refer to increased capacity and extra life. We also use a C3 fit bearing which has a larger than normal internal radial clearance which is optimal for vibratory duty applications.
Custom Solutions
Hindon, with the support of Invicta Vibrators, provide custom solutions that take into account high temperature or heavy loaded, high speed applications.
For example, we often suggest brass caged bearings in foundry applications because of higher than normal ambient operational conditions. Also, some higher speed, higher force output Invicta Vibrator models use brass-caged bearings as standard for applications such as large compaction tables, bin activators, and bin dischargers.
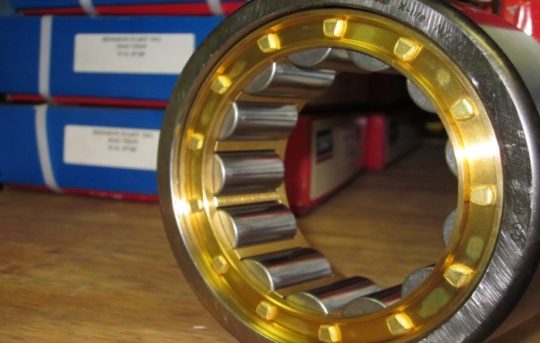
Brass caged bearings provide extra life in challenging applications and environments.
Grease Overview
Bearing grease is made up of two primary components – oils and wax thickeners (soap). Bearing grease is critical because it provides a barrier between two metal surfaces (the rollers and the inner race) from coming into direct contact with each other. The oils provide this “buffer” and the thickening agent is used to maintain grease consistency.
Factory-Specified Grease
As with bearings, it’s critical to use the factory recommended grease. Mixing greases of different compounds will change the chemical composition of the grease and lead to run-out or thinning of the grease leaving metal surfaces unprotected and prone to wear and corrosion.
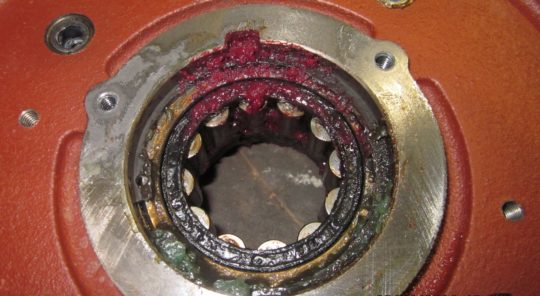
Mixing greases results in a separation of the oils from the thickeners leaving the bearing rollers exposed.
Hindon/Invicta Standard Grease
Invicta Vibrators factory specified bearing grease is Exxon Mobil Unirex NLGI2 or NLGI3 (N2 or N3) grease. This lubricant is lithium-based and light green in color. In addition to being suitable for operating at a wide range of ambient temperatures, Unirex N2/N3 is also resistant to water and corrosion and therefore provides for a long service life in vibratory equipment.
Bearing Maintenance
Once you’ve taken the steps to avoid premature bearing failures (e.g., using the wrong bearings or grease), it’s now time to dig into bearing maintenance. Proper bearing maintenance is critical to getting the maximum life out of your vibrator, as bearings are the most important wear item on a heavy-duty rotary electric vibrator.
Keep Contaminants Out
The number one priority in terms of bearing maintenance for industrial vibrators is keeping contaminants out.
When contaminants enter the bearing cavity they can mix with the grease and break down its chemical composition, resulting in premature run out. Even worse, the foreign material can make the grease gritty and abrasive, causing the bearing rollers to skid along the bearing inner race.
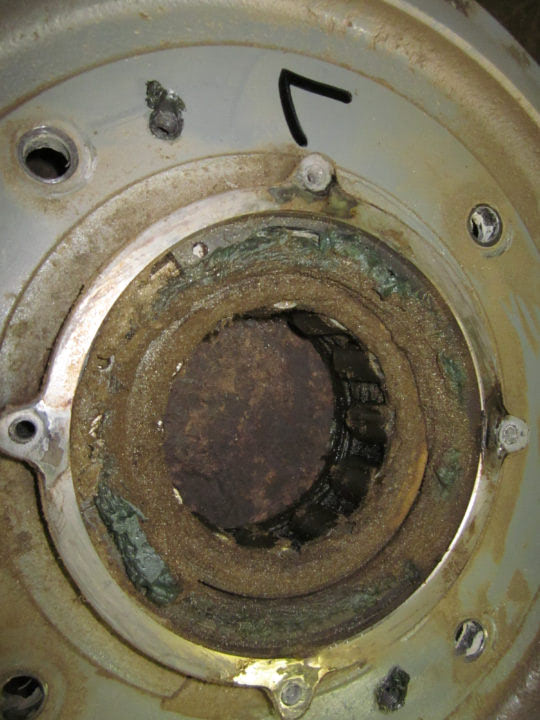
External contaminants (in this case a very fine sand) that enter into the bearing cavity will mix with the grease and cause it to break down, essentially eliminating all of the oils, leaving no barrier between the metal rollers and inner races.
Ensure Hardware is Properly Installed
Most Invicta vibrators are IP66 rated which means they are dust proof and water tight. That doesn’t necessarily mean, however, that contaminants cannot get into the vibrator when misapplied.
It is imperative that the sealing rings from the bearing housing flange to the end cover are correctly in their groove and that all end cover bolts are properly fastened.
Laminar rings, or grease retaining seals, also help keep dirt and other contaminants out of the bearings. Laminar rings are a type of split ring that wraps around the rotor shaft between the bearing housings and winding. This hardware essentially creates a labyrinth that allows spent grease to bleed out of the housings to the shaft extension. It also provides an effective barrier when new lubrication is introduced, making sure that it is directed into the bearing rather than moving inside to the winding cavity.
Avoid Contamination When Relubricating
It is also critical that you avoid introducing contaminants into your grease during the relubrication process.
To help avoid this surprisingly common issue, we recommend relubricating your industrial vibrator with a dedicated grease gun. The N2 grease is supplied in standard 14 oz tubes, so it’s easy to install in a grease gun and set aside for dedicated use.
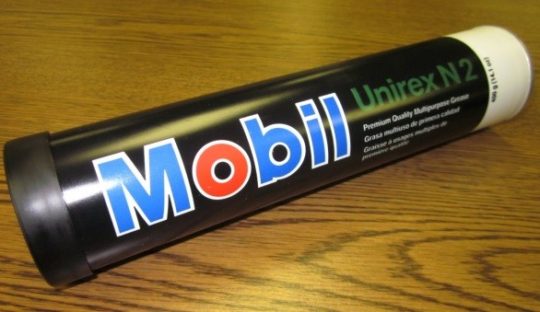
Using an N2 grease in a dedicated grease gun is one of the best ways to ensure you aren’t introducing contaminants when relubricating your industrial vibrator.
The N3 grease, however, can be slightly more difficult to apply. Because the N3 is thicker than N2, it is supplied in a 35 lb. pail and thus has to be manually packed into a grease gun and then pumped into the grease fittings of the vibrator.
Always remember to pack the grease gun in a clean area, away from the dust particulates that may be airborne around the vibratory equipment. It is also critical that the grease fittings on the vibrator be wiped down and clean prior to introduction of new grease.
Custom Solutions
We have also implemented custom sealing solutions/additions in situations where the standard sealing arrangement may not be enough or where plant circumstances require it. For example, we can add secondary internal or external sealing arrangements including v-rings (where not already offered as standard), labyrinth seals, and additional flange seals.
Relubrication Interval
Establishing a preventative maintenance schedule that calls for the correct relubrication interval and grease amount is also critical to maximizing the life and performance of your industrial vibrator.
Avoid Under-Greasing
Too little grease is bad is bad because bearings require a layer of film between the rollers and inner races. If there is not enough grease coverage, you will start to experience metal-to-metal contact between the surfaces which will lead to skidding, brinelling, and, ultimately, bearing failure.
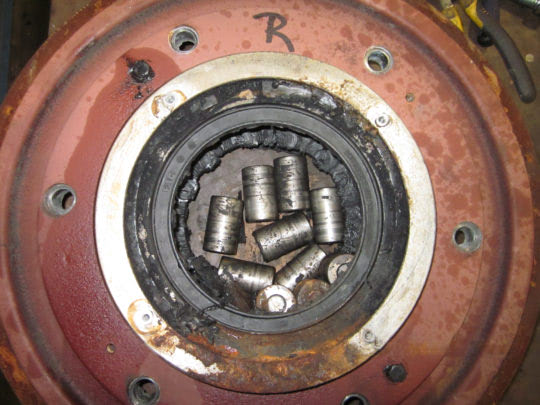
This bearing ran dry for long enough to completely break apart the polyamide cage.
Avoid Over-Greasing
Putting too much grease in your vibrator can also create problems. Over-greasing mostly manifests itself through higher running temperatures and amperage draws which can electrically fail the vibrator. The photos below illustrate an extreme case of over-lubrication:
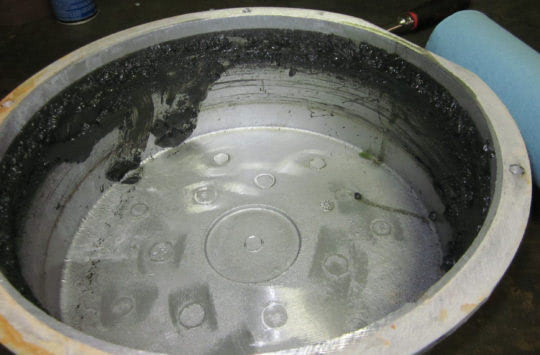
Large amounts of excess grease in the end cover is a common sign of over-lubrication of the vibrator bearings.
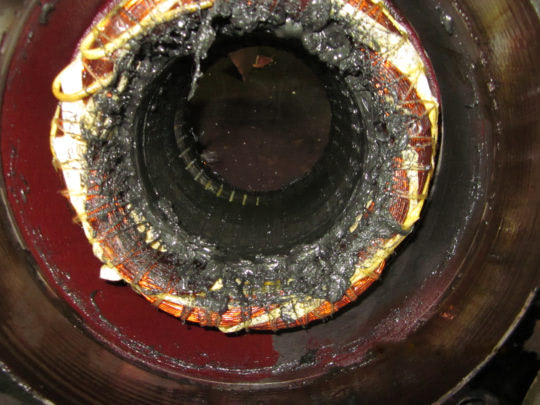
While the vibrator is designed to direct grease to the bearing cavity and away from the winding, these mechanisms can fail in the case of extreme over-lubrication. Grease in the winding cavity can breakdown the insulation causing a short to ground.
Standard Relubrication Interval
Each bearing size and rotational speed will have different requirements for amount of grease and relubrication interval. Typically, vibrators operating at faster rotational speeds will require more grease more frequently. The below table represents the relubrication intervals and amounts for our standard “L” series vibrators:
Click here for PDF of Bearing Relubrication Intervals
Adjust for Hot Ambient Conditions
The optimal relubrication interval is largely dependent on ambient conditions. If the equipment is operating in an area that is very hot (ambient conditions consistently above 80° F) then you likely need to relubricate more often – just how often can be determined by applying a temperature-based multiplier to the standard relubrication interval.
As a simplified example, consider a foundry with vibratory equipment that is used to handle very hot material. Assume temperatures around the equipment are consistently around 95°F. The foundry is using Invicta Model BL 50-75/6, which has a standard relubrication interval of 1.3 Oz of grease every 3,400 hours. Because of the high ambient temperature and arduous duty cycle, the bearings are experiencing a higher than normal amount of “oil bleed.” As such, we recommend a 0.5 multiplier be applied to the standard 3,400 hour re-lubrication interval. This means this foundry customer will want to relubricate their vibrator bearings every 1,700 hours using the standard 1.3 Oz per bearing amount.
Calibrate Your Grease Gun
Another benefit of using a dedicated grease gun is that it helps you be more certain and precise about how much grease you’re applying when you relubricate your vibrating motor. While some grease guns or auto lubricators are sophisticated enough to tell you exactly how much grease is being introduced, many times the best way to know is by simply measuring it yourself using a scale and cup.
Custom Solutions
The team here at Hindon is more than happy to custom tailor a relubrication interval specific to your needs using your exact duty cycle and ambient conditions.
Expected Bearing Life
L-10 Life
Bearing L-10 life (sometimes referred to as B-10 life) is an interesting topic as it relates to industrial vibrators. L-10 life represents the number of hours that 90% of bearings (of equal size) will operate before metal fatigue develops. This is important because it gives you an idea of how much life to expect out of the bearings before replacement is required.
The limitation of relying on L-10 for industrial vibrators is that these values are based on perfect theoretical operating conditions (i.e., adequate and consistent lubrication, no contaminants, no abnormal heat, etc.). However, heavy-duty rotary electric vibrator motors are often used in extremely arduous environments. Therefore, even when conditions are more moderate, they are rarely the “perfect” conditions assumed when a bearing’s L-10 life is determined.
Application-specific factors also impact L-10 life. In general, the faster the speed and higher the load (maximum force output), the lower the L-10 life will be. Conversely, a slower rotational speed with relatively low force will have a much higher L-10 life.
For example, Invicta Model BL 60-90/8 will have an L-10 life of greater than 100,000 hours, but a BL 40-30/2 will have less than 30,000 hours because of it’s high operational speed and relative high centrifugal force output.
Lastly, if you are not utilizing the maximum CF output of a given vibrator (i.e., setting your out-of-balance weights to a minimum setting), you should expect to see a much higher L-10 life.
“Sealed for Life”?
One of the buzzwords going around in the industry right now is “sealed for life” bearings. The reality is the only true sealed for life bearings are sealed ball bearings, which are not ideal for use in larger rotary electric vibrators. All cylindrical roller bearings will require relubrication after some period of time.
Don’t be fooled by this statement. If you expect minimal life out your bearings or vibrator, and don’t expect to make it past the first relubrication interval, then perhaps you can consider your vibrator bearings sealed for life. That said, we think you should expect more about of your industrial vibrator and proper bearing maintenance and relubrication is just part of that process.
__
So there you have it – bearing maintenance is not rocket science, but if neglected or misunderstood, it will lead to unexpected machine downtime and shorter machine life than you deserve.
We’d love to hear from you. We encourage you to reach out to the team here at Hindon if you have any questions or comments about this blog, other common industrial vibrator issues, or anything related to your vibratory application.