Industrial vibrators are unique pieces of equipment. While often associated with electric motors, industrial vibrators have vastly different mechanical and electrical characteristics and can wreak havoc on your operation if misapplied and misunderstood. So that you know what to look for, below are the most common causes of failure that we see:
Improper Mounting

Visible abrasion of pedestals, also known as “pitting”, is a common sign of improper industrial vibrator mounting
Proper mounting is where it all starts. Industrial vibrators are designed to shake themselves (and the structure of your vibratory equipment) into pieces if not properly installed. Improper mounting can manifest itself in a number of ways and is often the root cause of a number of common failure modes. It’s all about having a rigid and flat base to which to mount the vibrator, having full contact between the base and the vibrator pedestals, and securing the motor with proper torque and hardware.
Click here for more detail on how to properly mount your industrial vibrator.
Improper Sizing
An industrial vibrator needs to be properly sized relative to the equipment and application. If not, at best you’re losing efficiency, and at worst you will fail more than just the vibrator. A number of factors go into determining the most appropriate vibrator depending on application specifics and what you are trying to accomplish. Each unique application (e.g., screening, feeding, compacting, flow-aids, etc.), not to mention different types of materials handled, will all require slightly different sizes, speeds, and centrifugal forces. The application experts at Hindon are well equipped to customize an industrial vibrator specific to your requirements.
Click here for more detail on how to specify the right rotary electric vibrator.
Improper Lubrication
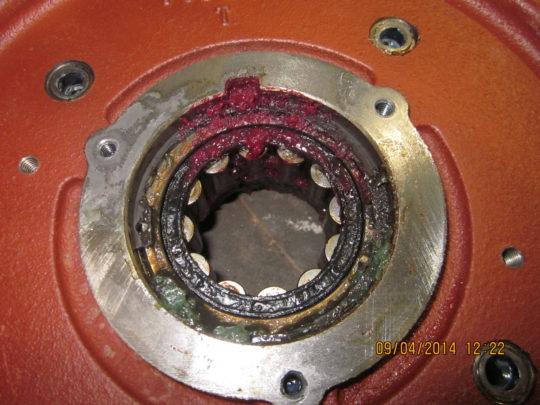
Mixing can compromise the performance of both lubricants and result in premature oil bleed
The life of an industrial vibrator depends on its bearings, and the life of the bearings depends on its lubrication. It’s critical that a consistent re-lubrication schedule be maintained according to the bearing size, duty cycle of the vibrator, and ambient conditions around the equipment. It’s also very important that the correct, factory specified bearing grease be used and different compounds of greases should not be mixed. It’s best to have a dedicated grease gun to be specifically used for your Invicta Vibrators.
Click here for more detail on industrial vibrator bearings including maintenance tips.
Electrical Overloads
The most common type of electrical failure we see is complete overloads. This can happen with voltage surges in the electrical system, or when there is another mechanical problem that has not been addressed. This is why it’s critical that thermal overload protection be used in your control panel. Invicta Vibrators are also equipped with PTC sensors, or thermistors installed in each winding phase. These sensors will provide motor protection against thermal overheating and are highly recommended to be used in conjunction with an electronic control module.
Not Holding a Spare
We are committed to serving our customers’ industrial vibrating motor needs and we understand the importance of avoiding downtime. That’s why we stock a wide range of Invicta Vibrators, including alternative footprint models & UL certified explosion proof units, ready to ship the same day, at our facility in Charleston, SC. We’ll always do our best to get you back up and running and can work with you on maintenance schedules and vibrator repairs. If your operation depends on a vibrating motor, we believe it’s a mistake not to hold a spare.